Welding Skid Solutions: Boost Your Efficiency on Site
A welding skid is a portable platform designed for welding tasks in various environments. It allows easy transport and setup of welding equipment.
Welding skids are essential for professionals who require flexibility and efficiency on job sites. These platforms provide a stable base for welding machines, tools, and materials. Their mobility makes it easy to move between locations, whether in a workshop or on a construction site.
Many models feature integrated storage for gas tanks, cables, and other accessories, enhancing organization and safety. The design often includes rugged wheels for smooth transport across uneven terrain. With various sizes and configurations available, users can choose a welding skid that meets their specific needs, ensuring optimal performance and convenience during welding projects.
Introduction To Welding Skids
Welding skids are essential tools in construction projects. They provide a stable platform for welding tasks. These skids support both the welder and the materials. Understanding their role helps in improving efficiency on job sites.
The Role Of Welding Skids In Construction
Welding skids play a crucial part in construction. They offer several advantages for welders and projects:
- Stability: They keep materials secure during welding.
- Mobility: Skids can be moved easily across sites.
- Versatility: Suitable for various welding tasks.
- Safety: Reduce risks of accidents on site.
Using welding skids enhances the quality of work. They help welders focus on their tasks without distractions.
Benefits Of Using Welding Skids On Site
Welding skids provide several benefits:
Benefit | Description |
---|---|
Increased Efficiency | Welders work faster with stable setups. |
Improved Quality | Stable platforms lead to better welds. |
Cost-Effective | Reduce rework and material waste. |
Enhanced Safety | Minimize accidents and injuries on site. |
Welding skids streamline processes. They contribute to a safer, more productive work environment.
Key Components Of Welding Skids
Welding skids are essential for efficient welding operations. They house various components that improve mobility and functionality. Understanding these key components helps in selecting the right skid for your needs.
Understanding Skid Frame Structures
The frame is the backbone of a welding skid. It provides support and stability. Key features include:
- Material: Usually made of steel or aluminum.
- Design: Must accommodate various welding equipment.
- Mobility: Equipped with wheels for easy transport.
These features enhance the skid’s durability and efficiency. A strong frame prevents equipment damage during movement.
Essential Welding Equipment
Welding skids contain vital equipment for welding tasks. Important tools include:
- Welding Machine: The primary tool for joining materials.
- Gas Cylinders: Provide fuel for welding processes.
- Welding Accessories: Include hoses, regulators, and clamps.
- Safety Gear: Helmets, gloves, and protective clothing.
Each component plays a critical role in welding operations. Proper arrangement ensures safety and efficiency.
Component | Function |
---|---|
Welding Machine | Joins materials through heat and pressure. |
Gas Cylinders | Supply gas for welding processes. |
Welding Accessories | Support welding operations with necessary tools. |
Safety Gear | Protects the welder from hazards. |
Understanding these essential components aids in effective welding. Choose the right skid for your projects to ensure success.
Customization Options For Welding Skids
Welding skids offer various customization options. These features help meet specific project needs. Tailoring these skids can greatly enhance efficiency and performance.
Tailoring To Project Needs
Every welding project is unique. Customization ensures the skid fits perfectly. Here are common options:
- Size and Dimensions: Modify the length and width.
- Weight Capacity: Adjust for heavier loads.
- Tool Mounts: Add specific mounts for tools.
- Storage Solutions: Include racks and compartments.
These options allow for better organization and efficiency. Each project can have its own tailored skid.
Modular Design Features
Modular designs offer flexibility. Users can adapt the skid as needed. Key features include:
Feature | Description |
---|---|
Interchangeable Parts | Swap out components easily for different tasks. |
Expandable Sections | Add or remove sections based on project size. |
Customizable Attachments | Use specific attachments for different welding techniques. |
Modular designs enhance versatility. Users can create the perfect setup for any welding task.
Efficiency Gains With Welding Skids
Welding skids enhance productivity in various projects. They simplify processes, leading to significant efficiency gains. Teams can work faster and smarter with these tools. Discover how welding skids transform on-site workflows.
Streamlining On-site Workflow
Welding skids offer clear benefits for on-site operations. They provide a compact and organized workspace. This structure helps workers find tools quickly.
- Improved organization: All tools and materials stay in one place.
- Easy access: Workers can reach equipment without delay.
- Reduced clutter: A clean workspace promotes safety and efficiency.
With a streamlined workflow, teams can complete tasks faster. This leads to timely project delivery and satisfied clients. Welding skids transform chaotic sites into well-organized environments.
Reduction In Setup And Dismantling Times
Setup and dismantling take valuable time. Welding skids minimize these durations significantly. Here’s how:
Process | Traditional Method (Hours) | With Welding Skids (Hours) |
---|---|---|
Setup Time | 3 | 1 |
Dismantling Time | 2 | 0.5 |
Welding skids cut setup time by up to 66%. Dismantling time decreases by 75%. This efficiency allows teams to focus on welding tasks.
- Faster project completion: Less time spent on setup means more work done.
- Increased productivity: Workers can weld more in less time.
- Cost savings: Reduced labor hours lead to lower project costs.
Embracing welding skids is a smart choice for any project. These tools boost efficiency, save time, and enhance productivity.
Safety Enhancements
Safety is the top priority in any welding operation. A Welding Skid must include safety features. These enhance protection for users and equipment. Implementing effective safety mechanisms reduces accidents. Compliance with industry standards is vital for ensuring safety.
Incorporating Safety Mechanisms
Many safety mechanisms exist for welding skids. Here are some essential features:
- Emergency Stop Button: Instantly halts operations.
- Protective Shields: Guards against sparks and debris.
- Fire Extinguishers: Readily available in case of fire.
- Training Programs: Ensure all users are well-trained.
These mechanisms help create a safer work environment. Regular maintenance of these features is crucial. Inspect them frequently for optimal performance.
Compliance With Industry Standards
Following industry standards is essential for safety. Compliance ensures that all equipment meets safety requirements. Key standards include:
Standard | Description |
---|---|
ANSI Z49.1 | Guidelines for safe welding practices. |
OSHA Standards | Regulations for workplace safety. |
ISO 3834 | Quality requirements for welding processes. |
Adhering to these standards protects everyone involved. Regular training updates ensure workers stay informed. Check for compliance often to maintain safety.
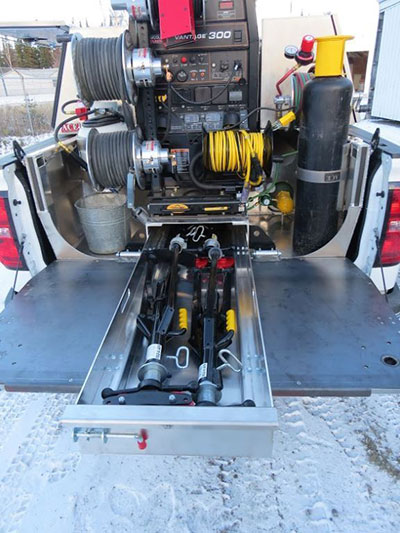
Credit: acemfginc.com
Mobility And Transportation
Welding skids are designed for easy mobility and transportation. They simplify movement between job sites. This feature enhances efficiency in various environments.
Ease Of Relocation
The design of welding skids makes them simple to relocate. Users can move them quickly without much effort. Here are some benefits:
- Lightweight materials facilitate quick transport.
- Built-in handles improve grip during movement.
- Compact size fits in tight spaces.
Welding skids often come with wheels. This allows for smooth movement across different surfaces. Users can set up quickly at new locations.
Compatibility With Various Transport Modes
Welding skids work well with many transport options. They can be transported by:
- Trucks
- Trailers
- Forklifts
Here’s a quick look at compatibility:
Transport Mode | Advantages |
---|---|
Trucks | Easy loading and unloading. |
Trailers | Large capacity for multiple skids. |
Forklifts | Fast movement across job sites. |
These features make welding skids a versatile solution for professionals. They enhance productivity on any job site.
Maintenance And Upkeep
Proper maintenance and upkeep of your welding skid ensure its longevity and efficiency. Regular care can prevent costly repairs and downtime. Here are some essential tips for maintaining your equipment.
Routine Maintenance Tips
- Inspect Daily: Check for any visible damages or wear.
- Clean Regularly: Remove dirt and debris from surfaces.
- Check Fluid Levels: Ensure fuel, oil, and coolant levels are adequate.
- Inspect Connections: Look for loose or corroded electrical connections.
- Test Safety Features: Ensure all safety mechanisms function correctly.
- Lubricate Moving Parts: Use the recommended lubricant to prevent friction.
Long-term Care For Welding Skids
Long-term care of your welding skid requires a few extra steps. These actions can help maintain performance over time.
Action | Frequency |
---|---|
Full Inspection | Every 6 months |
Oil Change | Every 100 hours of operation |
Battery Check | Every 3 months |
Replace Filters | Annually |
Follow these long-term care practices:
- Store Properly: Keep the skid in a dry, safe place.
- Protect from Elements: Use covers to shield from weather.
- Maintain Documentation: Keep a log of all maintenance activities.
- Train Staff: Ensure operators understand maintenance needs.
Regular maintenance ensures your welding skid operates smoothly and efficiently.

Credit: m.youtube.com
Case Studies
Case studies reveal the real-world benefits of using a welding skid. They showcase how different industries achieve efficiency and cost savings. Let’s explore some success stories and compare results before and after implementing welding skids.
Success Stories In The Field
Many companies have transformed their operations with welding skids. Here are a few notable examples:
- Company A: Reduced project time by 30% using a portable welding skid.
- Company B: Saved $50,000 annually on labor costs.
- Company C: Improved weld quality by 25% with advanced technology.
These stories highlight how welding skids enhance productivity. They also show significant cost reductions and quality improvements.
Comparative Analysis Of Pre And Post Welding Skid Implementation
To understand the impact, let’s look at a comparative analysis.
Metric | Before Welding Skid | After Welding Skid |
---|---|---|
Project Time | 40 hours | 28 hours |
Labor Costs | $1,500 | $1,000 |
Weld Quality | 70% | 95% |
This table illustrates clear benefits. Companies experience reduced project time, lower costs, and better quality. Welding skids contribute significantly to operational efficiency.
Future Of Welding Skids
The future of welding skids looks promising. New technologies will enhance efficiency and safety. Innovations will change how welding is done on-site. Let’s explore what awaits in this exciting field.
Innovations On The Horizon
New innovations are set to transform welding skids. Here are some key advancements:
- Automation: Robots will assist in welding tasks.
- Smart Technology: Sensors will monitor welding conditions.
- Lightweight Materials: New materials will reduce skid weight.
- Eco-Friendly Solutions: Sustainable practices will be prioritized.
These innovations aim to improve safety and productivity. They will reduce human error and enhance precision.
Predicting Industry Trends
Several trends are emerging in the welding skid industry. Here are some predictions:
- Increased Demand: Industries will require more portable solutions.
- Customization: Skids will be tailored to specific projects.
- Remote Monitoring: Operators can track projects from afar.
- Training Programs: Enhanced training will improve skills.
These trends highlight a shift towards efficiency and flexibility. The welding industry will adapt to meet new challenges.

Credit: www.reddit.com
Frequently Asked Questions
What Is A Welding Skid?
A welding skid is a portable platform designed for welding operations. It typically includes storage for equipment and tools. These skids enhance mobility and efficiency on job sites. They are ideal for various welding tasks, from construction to repairs.
Why Use A Welding Skid?
Using a welding skid improves organization and accessibility of equipment. It allows welders to work efficiently in diverse environments. The mobility of a skid makes it easier to transport tools. This versatility saves time and enhances productivity on projects.
What Materials Are Used For Welding Skids?
Welding skids are commonly made from steel or aluminum. These materials offer durability and resistance to harsh conditions. Steel skids provide strength, while aluminum skids are lightweight. The choice depends on the specific requirements of the welding job.
How Do I Maintain A Welding Skid?
Regular maintenance of a welding skid includes checking for rust and damage. Clean the skid after each use to prevent corrosion. Lubricate moving parts to ensure smooth operation. Inspect storage compartments for organization and safety.
Conclusion
Welding skids offer versatility and efficiency for various projects. They enhance mobility and accessibility in challenging environments. Investing in a quality welding skid can significantly boost productivity. Always choose a skid that meets your specific needs. With the right equipment, you can achieve exceptional results in your welding endeavors.